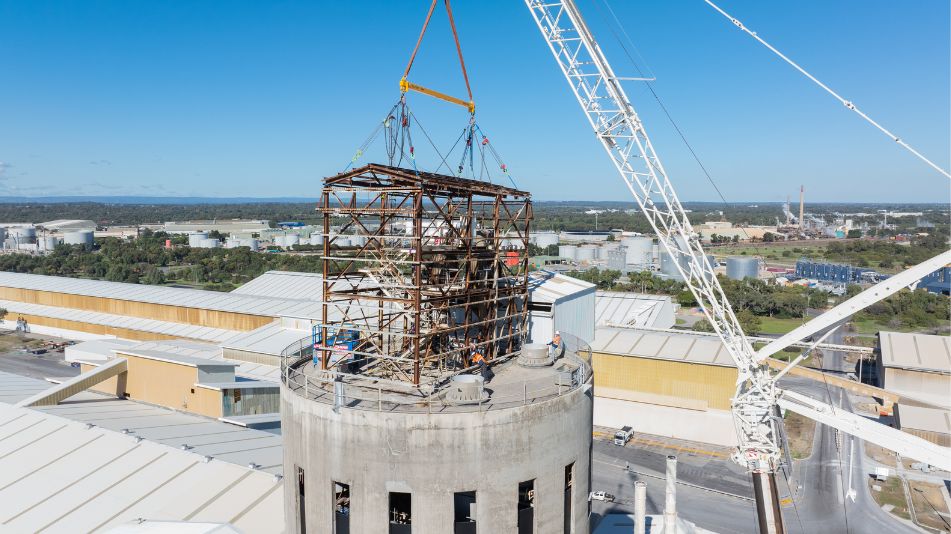
Risk Mitigation Strategies for Commercial Demolition Projects
If you’re planning a commercial or industrial demolition project, you already know the stakes are high. Safety incidents, project delays, community complaints, and unexpected structural issues can derail progress and drive up costs.
This article outlines key risk factors in commercial demolition projects and how to assess whether your demolition contractor has the expertise and systems in place to manage them.
Whether you’re still in early scoping or have actively started shortlisting demolition companies, use this as a practical guide to ensure your project is safe, compliant, and cost-controlled.
Understanding the Key Risks
Effective risk management in commercial demolition revolves around a few critical areas:
- Structural stability and how it affects demolition methodology
- Environmental compliance, including asbestos, contamination, and waste
- Regulatory obligations under the WHS Act 2020 and related legislation
- Impact on stakeholders, such as nearby businesses and infrastructure
By addressing these upfront, project managers and developers can reduce surprises, avoid liability, and keep timelines on track.
Regulatory Framework and Licensing Requirements
In Western Australia, most demolition projects are classified as “high risk construction work” under the Work Health and Safety Act 2020, particularly when they involve “demolition of an element of a structure that is load-bearing or otherwise related to the physical integrity of the structure” (Department of Energy, Mines, Industry Regulation and Safety).
This means most commercial demolition work in WA must be carried out by licensed demolition contractors. There are two main classes of demolition licences:
- Class 1 Demolition Licence: Required for complex demolition involving structures over 10 metres high, structural works, suspended floors, pre-tensioned concrete, or explosives.
- Class 2 Demolition Licence: Covers demolition of structures under 10 metres without structural complexity.
While it’s not mandatory to engage a licensed demolition contractor during early planning, doing so can help identify major risk areas before decisions are locked in—saving time and avoiding rework later.
At Focus Demolition, we hold a Class 1 Demolition Licence (WAD 223) and Class A Asbestos Removal Licence (WUA165). This qualifies us to manage the most complex and high-risk demolition and asbestos removal projects, including those in live, sensitive, or regional environments across WA.
Structural Assessment: Knowing What You’re Bringing Down
Before demolition, a licensed structural engineer should assess:
- Load-bearing elements and sequencing needs
- Structural ties to adjacent buildings
- Pre-tensioned concrete or steel under tension
- Risks during partial or staged demolition
Even with access to original plans, a new assessment should still be conducted. Buildings are often modified over time, and undocumented changes can create unexpected collapse risks.
Environmental Checks & Safeguards
Under WA’s Environmental Protection Act 1986, demolition must be managed to prevent pollution and harm. This includes:
- Comprehensive hazardous materials surveys (e.g. asbestos, lead, PCBs)
- Testing of soil and groundwater, especially on industrial sites
- Assessments for sensitive environmental zones nearby
- Site-specific dust and noise control plans
If your site is listed on the State Register of Heritage Places or is near environmentally sensitive areas (such as wetlands or conservation zones), additional planning approvals and documentation may be required. These can include archival recording, conservation advice, and conditions around structural salvage.
Stakeholder Management
A good demolition plan includes strategies for managing:
- Access for neighbouring businesses and vehicles
- Pedestrian protection (barriers, overhead gantries)
- Public communication and signage
- Noise, dust, and vibration controls
- Protection of nearby infrastructure (pipes, telecoms, etc.)
Ask your contractor: How do you communicate with surrounding tenants or councils before demolition begins?
Planning for Safe Demolition
Under WorkSafe WA guidelines and AS 2601, demolition contractors must prepare a site-specific Demolition Work Plan (DWP) that includes:
- Detailed demolition sequences that maintain structural stability
- Specific methodologies for different building elements
- Equipment selection based on structural and environmental factors
- Engineering controls for identified risks
- Unexpected finds protocols for hazardous materials
Before any commercial demolition project can begin, a thorough Safe Work Method Statements (SWMS) risk assessment must also be completed detailing:
- Step-by-step work procedures
- Specific hazards identified for each task
- Risk controls to be implemented
- Responsibilities for supervision and safety
- Emergency response procedures
This forms the foundation for all subsequent planning and site safety controls.
Managing Service Disconnections
- Unexpected live services are one of the most common causes of demolition-related incidents. Before any works begin, contractors should:
- Verify disconnections in writing from all relevant service providers
- Map any undocumented or unknown services—especially common in older buildings
- Coordinate timing with utility companies to avoid disruption or unsafe conditions
Demolition must not commence until all essential services are either fully disconnected or clearly isolated and protected.
Choosing the Right Equipment and Methodology
Every demolition site has its own risks, constraints, and engineering challenges.
Knowing how to choose the best equipment and methodologies for the job can make all the difference in mitigating site-specific risks. For instance:
- High-reach excavators reduce the need for personnel to work at height
- Hydraulic attachments help manage vibration and structural control
- Remote-controlled machines allow safe operation in unstable or restricted areas
- Water suppression systems are essential for dust and air quality management
Matching equipment and methodology to site conditions helps reduce risk, protect workers, and streamline project delivery.
Unexpected Finds Protocols
Even with thorough assessments, demolition sites often reveal undocumented hazards such as asbestos, underground tanks, or chemical residues. A professional demolition contractor will have contingency plans in place, including:
- Immediate site stop procedures
- Engagement of licensed specialists (e.g. hygienists or environmental consultants)
- Notifications to relevant authorities (e.g. WorkSafe or DWER)
- Revised SWMS and DWP updates
Choosing the Right Demolition Partner
Strong risk management starts with choosing a contractor who understands the full complexity of commercial demolition. At Focus Demolition, we don’t just meet compliance requirements – we set the benchmark.
We prioritise the safety of our team, clients, and the public above all else, working to the strictest safety protocols and investing continuously in training, equipment, and planning systems. Whether the project is high-risk, time-sensitive, or in a live environment, we have the experience and licensing to deliver it safely and efficiently.
Planning a commercial or industrial demolition project? Contact Focus Demolition to discuss your site and how we can support your risk management strategy from day one.